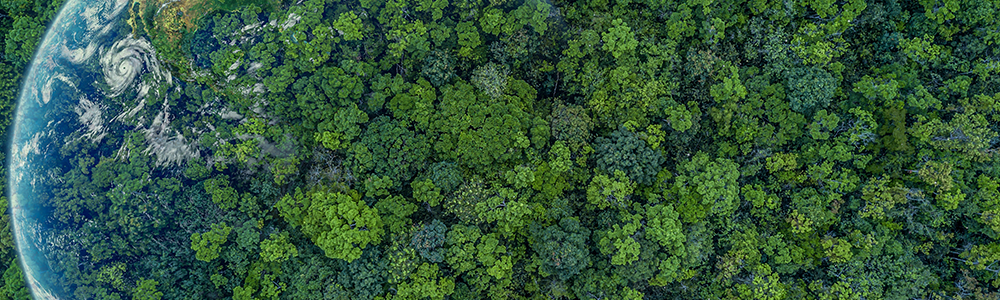
4 October 2023
Alternative Technologies to High-pressure Mercury Short Arc Lamps for Photolithography of Printed Circuit Boards (PCBs)
Photolithography for the manufacture of semiconductors and printed circuit boards (PCBs) is another major application for mercury lamps classified under item 4(f) in the exemption list of the RoHS Directive. This is in addition to curing and photolithography for the manufacture of liquid crystal displays (LCDs), which were described in the previous posts.
Photolithography is a lithography process in which a substrate coated with resist is exposed to light or an electron beam to draw a designed circuit. High-pressure mercury short arc lamps have been mainly used as the light source.
High-pressure mercury short arc lamps contain mercury, an environmental pollutant. Solid-state light sources such as LEDs and laser diodes (LDs) are expected to be used as alternative technologies. However, it was not easy for LEDs and LDs to produce the output required for photolithography and be equivalent to high-pressure mercury short arc lamps when the latest exemption was discussed several years ago. Therefore, in the RoHS Directive, the manufacture and sale of high-pressure mercury short arc lamps are allowed under the exemption until at least February 24, 2027, because no alternative technology has been established.
In addition to containing mercury, high-pressure mercury short arc lamps have several other practical problems when used in photolithography applications. First, it takes a few minutes to light up after the switch is turned on, making it not possible to have on-off control. This means that the switch must be left on constantly when the photolithography device is in operation. It also causes unstable and fluctuating light, which may affect the photolithography process. Furthermore, the lifetime of high-pressure mercury short arc lamps is only about 1,000 hours. If the lamps are used beyond their lifetime, they may become damaged and there is a risk that mercury is exposed. Therefore, they usually need to be replaced after about 2 or 3 months.
LEDs and LDs are expected to be an alternative technology that can not only contribute to making these applications mercury-free but also solve all these problems at once.
High-pressure Mercury Short Arc Lamps for Photolithography Applications → LD Adoption Case Studies
As explained above, there are several applications for photolithography using high-pressure mercury short arc lamps, including the manufacture of semiconductors and PCBs. This post will introduce an actual case study of LD adoption for photolithography of PCBs.
There are two types of photolithography devices for PCBs: those that use steppers and those that use direct imaging photolithography technology (DI). A stepper is a device that uses a photomask to produce a specific pattern, and light from a light source is projected onto a substrate through the photomask to transfer a fine pattern onto a printed circuit board. DI, on the other hand, does not use a photomask, it forms a pattern on the substrate by adjusting the lens to determine the location of the laser beam and directly exposing the pattern optically. DI has the advantage of reducing the time and cost required for designing and manufacturing photomasks and can be performed at extremely high speeds.
Stepper and DI Optical Configuration
For steppers, high-pressure mercury short arc lamps are still used in most cases because of their superiority in terms of resolution, etc. However, violet LDs emitting 405nm light, which is the wavelength for purple, are increasingly used as the light source for DI. Violet LDs, which emit 405nm light, began to be widely used as light sources for DI around 2000, and their output has been greatly improved over the past 20 years to 20 times the original output, together with improved productivity, ease of use, and many other advantages. For violet LDs to become the primary light source for all PCB photolithography devices, including steppers, further improvements are required, particularly in combination optics. This post will introduce an actual case study of LDs in DI where violet LDs are already used in most cases.
Figure 1. Comparison result: High-pressure mercury short arc lamps vs. Violet LDs
- This comparison result shows high-pressure mercury short arc lamps and LDs when used for photolithography of printed circuit boards (PCBs) using DI.
- CO2 emissions of 0.527t/MWh is the CO2 emission factor for FY2021 announced by Shikoku Electric Power CO., Inc.
In addition to meeting the initial goal of mercury-free by achieving equivalent photolithography as an alternative technology, violet LDs can also reduce power consumption and CO2 emissions because their power input is much less than that of high-pressure mercury short arc lamps. The required input power to achieve the same photolithography result is 1000W for high-pressure mercury short arc lamps for one standard photolithography device, whereas violet LDs are 300W. Assuming that both lamps are operated 24 hours a day for 340 days, the annual electricity consumption of high-pressure mercury short arc lamps is 8.2MWh, while that of the violet LD is 2.4MWh. Even without taking into account that the LDs can be quickly turned on and off, 70% can be saved.
CO2 emissions can also be calculated based on a CO2 emission rate of 0.527 tons per MWh of electricity consumption. The amount of CO2 emission by high-pressure mercury short arc lamps is 4.3t, while the amount of CO2 emission by the violet LD is 0.527t, achieving a similar reduction of 70%.
Furthermore, the lifetime of a violet LD is 40 times longer than that of high-pressure mercury short arc lamps, therefore also reducing the replacement frequency.
There are many benefits to replacing them with violet LDs besides being mercury-free.
Summary
Several years ago, when the current RoHS exemption was being considered, it was recognized that there was no alternative technology to replace high-pressure mercury short arc lamps for light sources in photolithography applications. Together with the actual case study of the UV LEDs for photolithography of LCDs introduced in the previous post, as for the photolithography of PCBs, violet LDs, another solid-state light source technology, has been clearly recognized as not only alternative but also offer significant benefits such as reduced power consumption and CO2 emissions through the recent rapid technological advances. This post also demonstrates an actual example where violet LDs were adopted at a manufacturing site.
Nichia believes that by further improving the performance of LEDs and LDs and discovering effective ways to use them by taking advantage of their respective characteristics, mercury lamps will be replaced with violet LDs in steppers and the extension of the RoHS exemption currently granted to mercury lamps will no longer be necessary for all photolithography applications.
Nichia continues to make efforts towards the realization of a mercury-free and carbon neutral society through the elimination of all mercury lamps.
For more information about products, please refer to Nichia's website.
Laser Diode (LD)